THE JOURNEY OF SHiP+AiD -PACKING-
Until SHiP+AiD Arrives
We present to you the process leading up to the delivery of "SHiP+AiD" to the vessel.
In the packaging phase, we meticulously ensure there are no errors in the product type, quantity shortage, or damages.
This is a humble yet crucial step to ensure our customers can use the product with peace of mind.
Protecting the Repair Material with Specialized Aluminum Cases
Upon thorough verification of the order details, the products are delicately housed in specialized aluminum cases.
These cases are designed not just as mere containers but as high-functionality tools to maintain the utmost quality of the products.
They are tailored for insulation and light-blocking properties, minimizing the risk of aging deterioration of the repair materials.
For instance, even under high-temperature conditions onboard or prolonged storage under direct sunlight, the repair materials inside the case remain stable.
Additionally, partition plates are installed inside the case, tailored to the size and shape of the repair materials, ensuring no disarray or mixing with other repair materials.


Quality Control through Diligent Work
We use cushioning materials to firmly protect the products, thus minimizing damage from vibrations and impacts during transportation.
Subsequently, the weight of the products is accurately measured, and they are carefully packed in cardboard boxes.
Especially when the delivery destination is distant or transportation requires several days, it's imperative to securely protect the products from humidity, external impacts, and temperature fluctuations.
The packaging task is not just a formal procedure but a highly significant operation to ensure the final quality of the products.
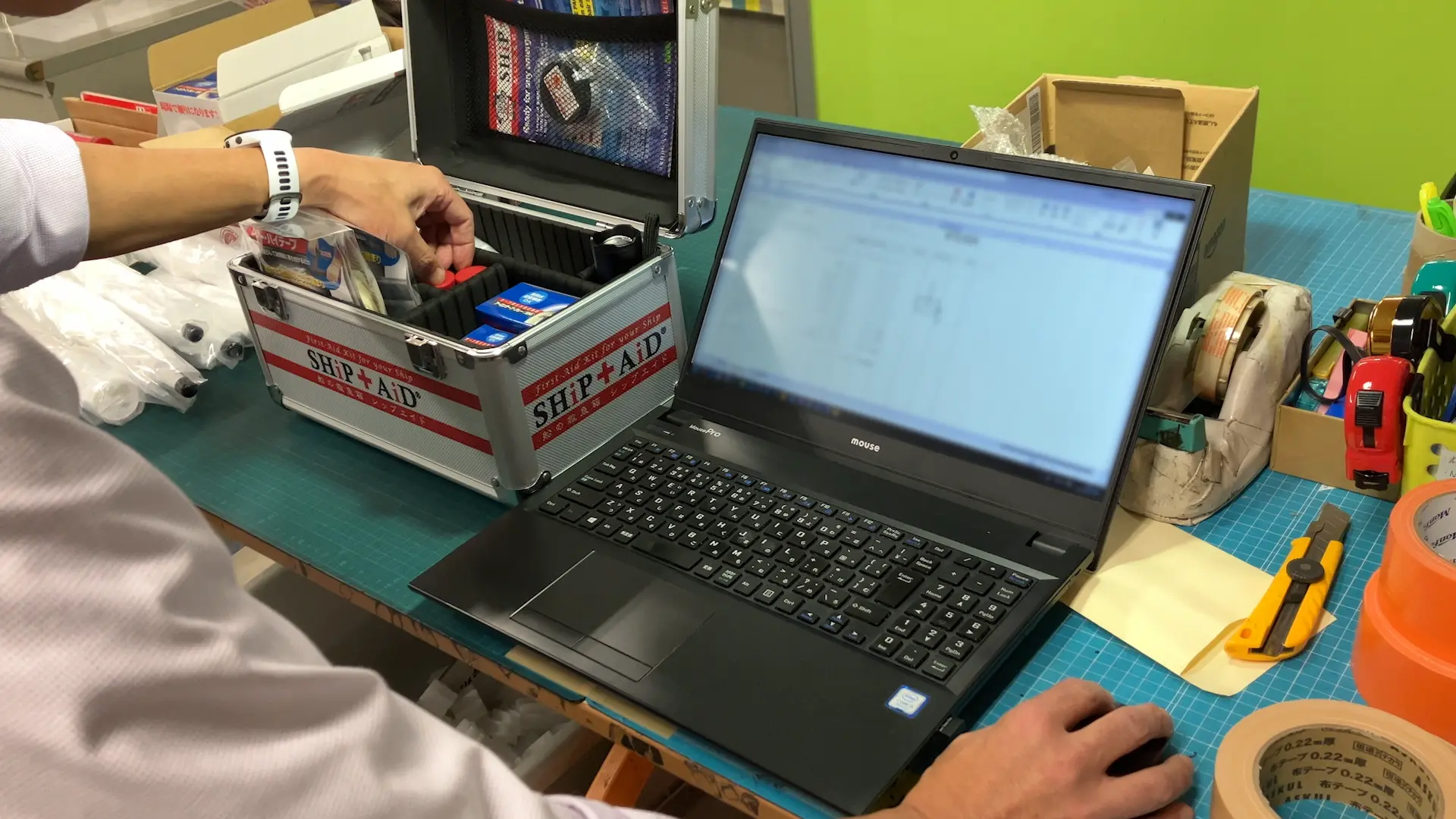
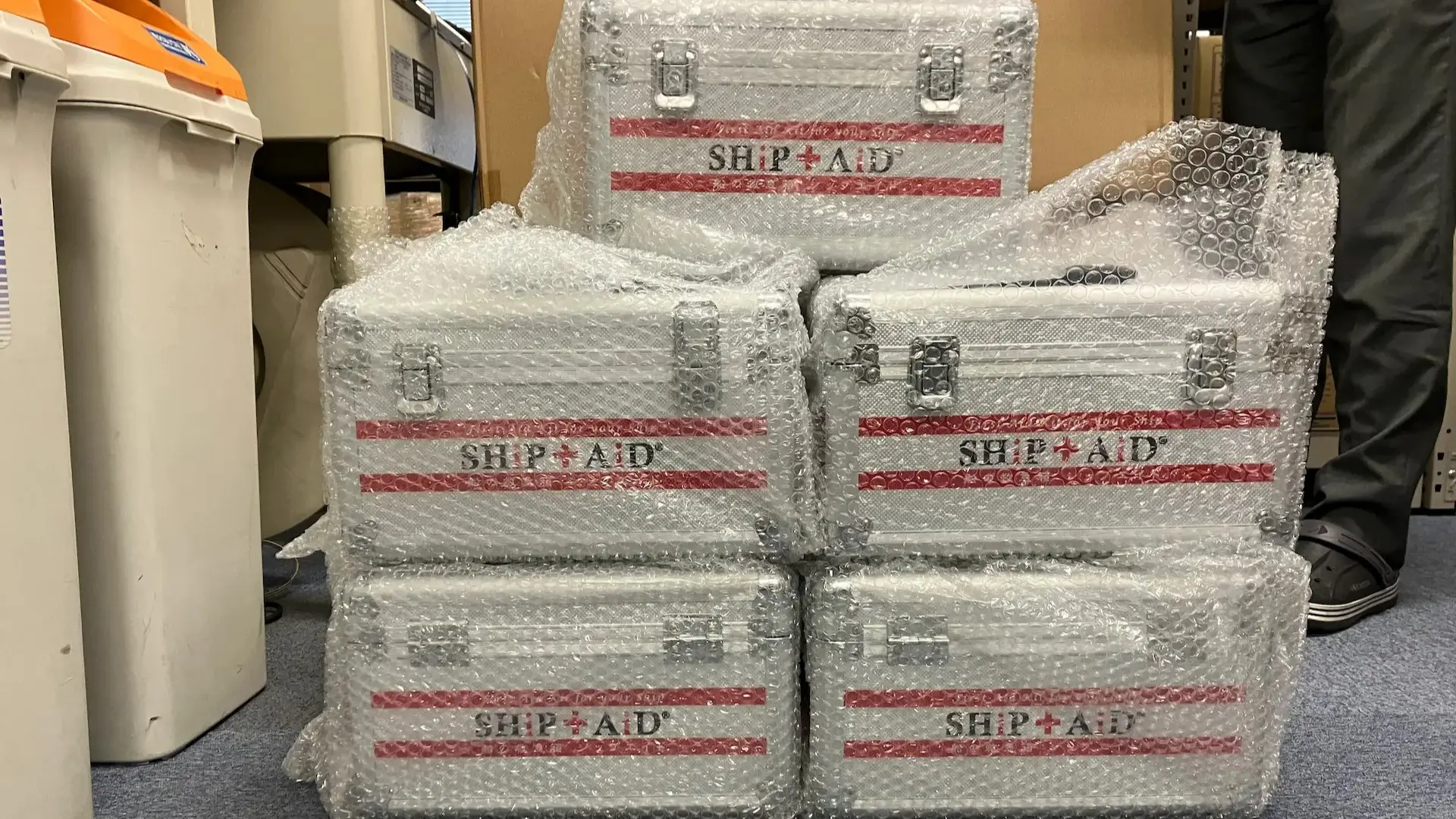
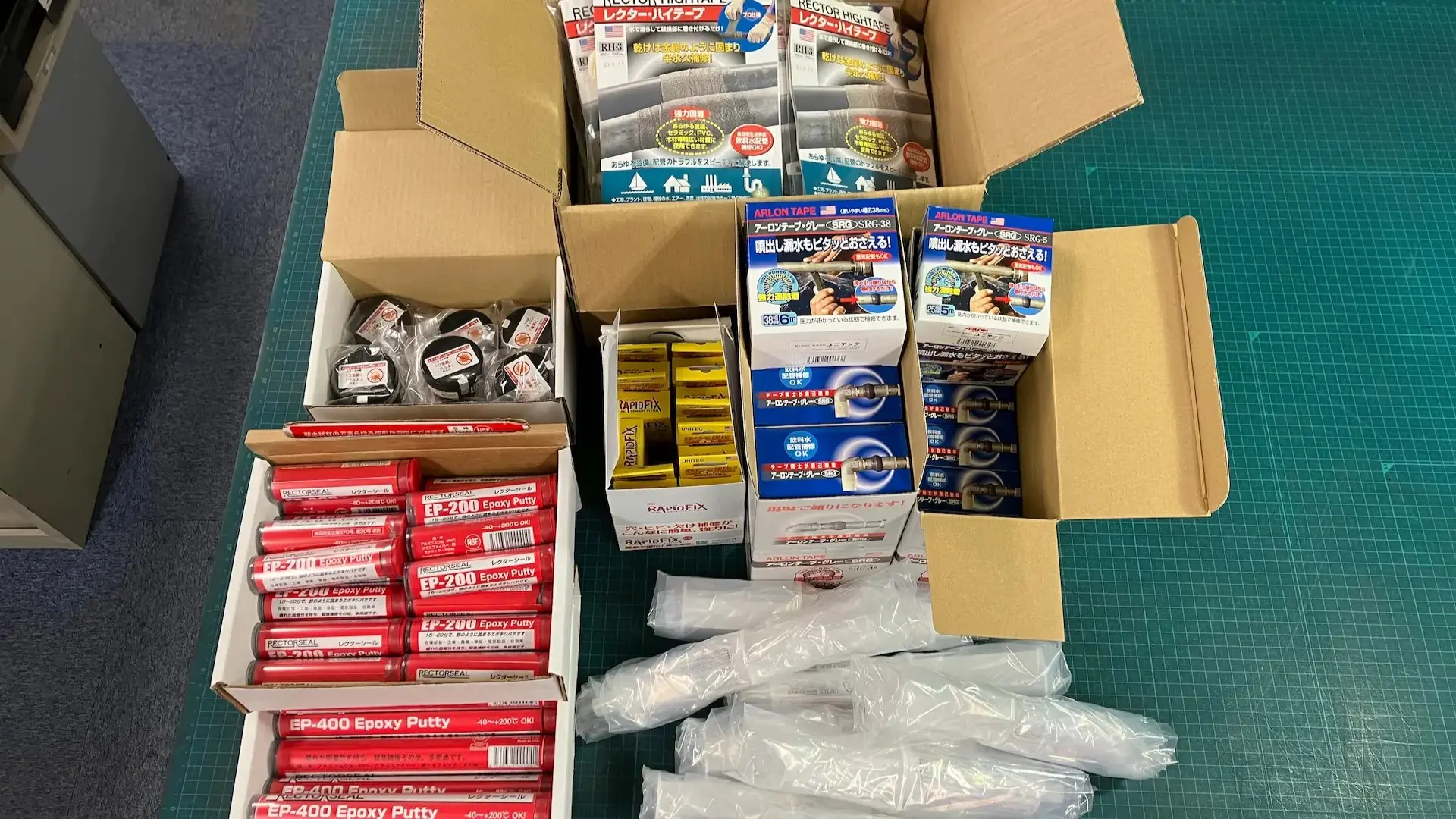